The “ooze electro barrel” presents a fascinating convergence of technology and material science. From its potential applications in advanced manufacturing to its intricate operational principles, this innovative device warrants careful examination. Understanding its design, manufacturing, and operational characteristics is crucial for assessing its viability and potential impact across various industries.
This exploration delves into the multifaceted nature of the ooze electro barrel, examining its diverse types, manufacturing processes, and real-world applications. We will analyze its operational mechanisms, highlighting the critical safety and maintenance considerations for responsible deployment.
Defining “Ooze Electro Barrel”
The term “ooze electro barrel” lacks a universally recognized, standardized definition within established scientific or engineering literature. Its meaning likely depends heavily on the specific context in which it is used, ranging from a hypothetical technological concept to a colloquial description of a particular design. Understanding its various interpretations requires examining potential applications and associated characteristics.The term might emerge in discussions about novel energy storage devices, futuristic concepts for materials science, or even as a playful description within a fictional setting.
Deconstructing the components and functionalities embedded within the term “ooze electro barrel” can reveal a deeper understanding of its underlying principles and potential applications.
Potential Interpretations of “Ooze Electro Barrel”
The term “ooze electro barrel” suggests a device that combines electrochemical processes with a fluid, potentially viscous, material. This implies a system capable of storing or generating energy through electrochemical reactions, potentially within a barrel-shaped structure. The “ooze” component hints at a liquid or semi-liquid medium, possibly with unique conductive or reactive properties. This contrasts with traditional electrochemical storage systems, which often utilize solid electrolytes or rigid containers.
Potential Contexts for “Ooze Electro Barrel”
The “ooze electro barrel” could be envisioned in several contexts:
- Advanced Energy Storage: The device might represent a futuristic energy storage solution, leveraging unique properties of the “ooze” to achieve higher energy densities or faster charging rates compared to existing battery technologies. Imagine a self-healing electrochemical system, capable of adapting to changing conditions and minimizing degradation.
- Materials Science Research: It could be a concept explored in the realm of materials science, examining the potential of novel electroactive materials within a fluid matrix. Researchers could be investigating the conductivity and reactivity of different “oozes” under various conditions, potentially leading to breakthroughs in energy storage and other applications.
- Science Fiction: In a fictional context, the “ooze electro barrel” might be part of a futuristic power source or a fictional technology that harnesses exotic electrochemical processes. This could be featured in a science fiction novel, movie, or video game, showcasing the imaginative possibilities of electrochemical engineering.
Key Characteristics and Components
The characteristics of an “ooze electro barrel” hinge on the specific interpretation and context. Common components and their functions are likely to include:
Component | Function | Material |
---|---|---|
Barrel Structure | Physical containment of the “ooze” and electrical components. | High-strength, corrosion-resistant polymer or metal alloy. |
Electroactive “Ooze” | Facilitates electrochemical reactions, potentially acting as an electrolyte or a reactive medium. | Composite material with electroactive components and conductive fillers. |
Electrodes | Enable electron transfer during electrochemical processes. | Conductive materials like carbon nanotubes or metallic alloys. |
Electrolyte | Conducts ions between electrodes, crucial for electrochemical reactions. | Specific material based on the “ooze” composition. |
Energy Output/Input Mechanism | Converts chemical energy to electrical energy or vice-versa. | Variable depending on the specific application (e.g., turbines, pumps). |
Types and Variations
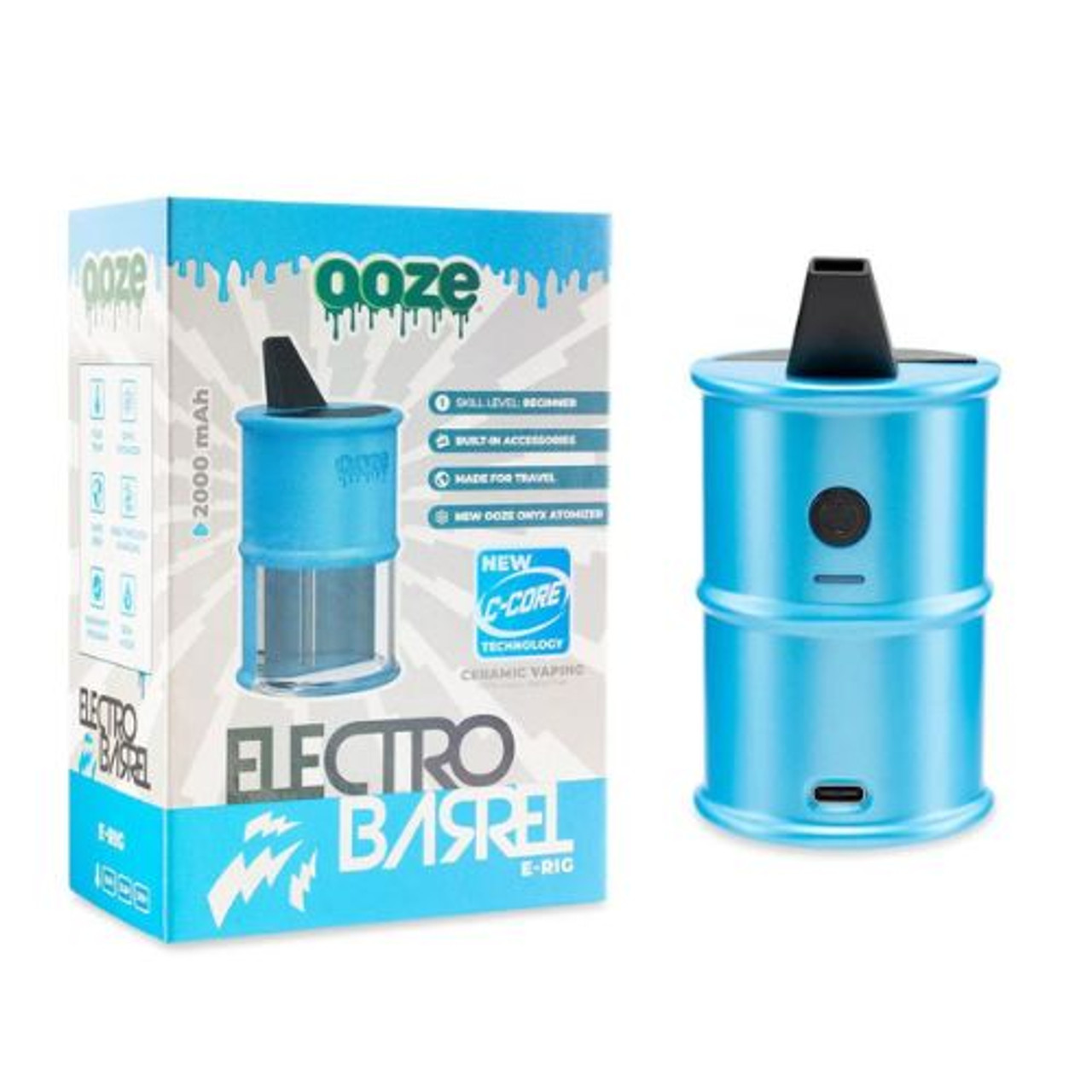
Ooze electro barrels, a burgeoning technology in energy storage, exhibit a diverse range of types, each optimized for specific applications. Understanding these variations is crucial for selecting the appropriate barrel for a given energy storage system. From material composition to dimensional specifications, the design nuances dictate the barrel’s performance characteristics and cost-effectiveness.The diverse types of ooze electro barrels are distinguished by their functional attributes, including the capacity to store and release electrical energy.
This categorization allows for precise matching of barrel type to specific energy demands, from small-scale applications to large-scale power grids.
Material Composition
Different materials influence the ooze electro barrel’s electrochemical properties, thermal stability, and overall lifespan. The selection of materials directly impacts the barrel’s energy density, charge/discharge rate, and safety characteristics. A higher energy density, for example, translates to greater energy storage capacity within a given volume.
- Carbon-based barrels, often employing activated carbon or graphene, are known for their high surface area, facilitating efficient ion transport and enhanced charge/discharge cycles. These are particularly well-suited for applications requiring rapid energy release, such as in electric vehicles.
- Metal-oxide barrels, leveraging materials like lithium cobalt oxide or nickel-manganese-cobalt (NMC) cathodes, are commonly used for their higher energy density. However, they may present challenges in terms of cost and safety considerations, requiring meticulous design for robust operation. The use of NMC in certain types of ooze electro barrels may enhance overall performance and efficiency.
- Polymer-based barrels, incorporating conductive polymers, provide a balance between energy density and cost-effectiveness. Their flexibility and lightweight properties make them suitable for portable energy storage devices.
Design Variations
Variations in barrel design significantly affect performance characteristics. These variations include modifications to the internal structure and external geometry. This includes the size, shape, and the manner in which the ooze electro-active material is distributed within the barrel, influencing the overall performance and efficiency of the barrel.
- Spiral-wound barrels, characterized by their coiled structure, offer a compact design that maximizes surface area for enhanced electrochemical reactions. This configuration can be particularly advantageous in space-constrained applications.
- Laminated barrels, composed of multiple layers of ooze electro-active material, enhance the barrel’s overall strength and stability. These barrels are typically more resilient to mechanical stress and offer improved structural integrity.
- Hollow-core barrels, with a central void, allow for better heat dissipation, mitigating the risk of thermal runaway during charging and discharging cycles. This characteristic is critical in high-power applications where rapid energy transfer is paramount.
Dimensional Specifications
The size and shape of ooze electro barrels directly impact their capacity and suitability for different applications. Larger barrels generally offer higher energy storage capacity, while smaller barrels are often preferred for portability and integration into compact devices.
Type | Description | Applications |
---|---|---|
Carbon-based Spiral-wound | High surface area, compact design | Electric vehicles, portable electronics |
Metal-oxide Laminated | High energy density, robust structure | Grid-scale energy storage, large-scale power systems |
Polymer-based Hollow-core | Lightweight, good heat dissipation | Wearable electronics, consumer electronics |
Manufacturing Processes
The manufacturing of ooze electro barrels, a specialized device for high-pressure applications, demands precision and meticulous control. Variations in design and materials directly impact the durability and performance of the final product. Understanding the manufacturing steps, material choices, and technologies employed is crucial for assessing the reliability and cost-effectiveness of these devices.
Materials Used
The selection of materials is paramount to the success of ooze electro barrels. Different materials offer varying degrees of strength, elasticity, and resistance to corrosion. The key materials typically include high-strength alloys, such as specialized steels and nickel-based superalloys, for the barrel’s structural components. These materials are carefully chosen to withstand the high pressures and temperatures encountered during operation.
Polymeric materials, such as reinforced polymers or composites, are often used for sealing elements and insulation layers, contributing to the barrel’s overall performance and longevity.
Construction Steps
The manufacturing process involves a series of carefully controlled steps. Initially, the chosen alloys are meticulously shaped into the desired barrel form using techniques such as precision machining or additive manufacturing (3D printing). These methods ensure precise dimensions and tolerances, crucial for maintaining the barrel’s structural integrity under pressure. Subsequently, the sealing elements and insulation layers are installed.
The process typically includes specialized welding or bonding techniques to ensure a hermetic seal and prevent leakage. Final quality control checks are implemented to guarantee the barrel’s functionality and safety before release.
Technologies Employed
Modern manufacturing technologies play a critical role in the production of ooze electro barrels. Advanced machining centers, equipped with sophisticated sensors and controls, are employed for precision cutting and shaping of components. Non-destructive testing (NDT) methods are utilized throughout the manufacturing process to identify potential flaws or imperfections in the materials and construction. Computer-aided design (CAD) and computer-aided manufacturing (CAM) software are instrumental in designing and optimizing the manufacturing process, reducing errors and improving efficiency.
Flowchart of Manufacturing Process
Step | Description |
---|---|
1. Material Selection | Selection of high-strength alloys and polymeric materials based on pressure and temperature requirements. |
2. Component Fabrication | Precision machining or 3D printing to shape the barrel and other components. |
3. Sealing Element Installation | Installation of sealing elements and insulation layers using specialized welding or bonding techniques. |
4. Quality Control | Non-destructive testing (NDT) to identify potential flaws and ensure structural integrity. |
5. Final Assembly | Assembly of all components into the complete ooze electro barrel. |
6. Testing and Certification | Comprehensive testing to validate performance and safety, including pressure and temperature tests. Certification is acquired as needed. |
Applications and Uses
Ooze electro barrels, with their unique electrochemical properties, are finding increasing applications across various industries. Their ability to efficiently process and transport specific materials opens doors to innovative solutions in sectors ranging from manufacturing to environmental remediation. These specialized barrels offer distinct advantages over traditional methods, often leading to enhanced efficiency and cost savings.The versatility of ooze electro barrels stems from their ability to facilitate electrochemical reactions within their internal structures.
This allows for precise control over material transport and transformation, enabling a wide range of applications, particularly in industries requiring controlled chemical processes. Their customized designs accommodate diverse needs, making them valuable assets in specific applications where efficiency and control are paramount.
Industrial Manufacturing
Ooze electro barrels are proving crucial in specialized manufacturing processes. Their controlled electrochemical environment allows for the precise deposition and shaping of materials, leading to enhanced product quality and reduced waste. This technology is particularly useful in industries dealing with intricate metal components, where precise control over the electrolytic process is essential. For example, in the production of microelectronic components, ooze electro barrels can facilitate the precise plating of metals, leading to smaller, more efficient circuits.
This targeted approach minimizes material loss and enhances the final product’s performance characteristics.
Environmental Remediation
Ooze electro barrels are showing promise in environmental remediation efforts. Their electrochemical properties allow for the targeted removal of contaminants from contaminated soil and water. In cases of heavy metal pollution, for instance, ooze electro barrels can facilitate the extraction of harmful elements, thereby minimizing environmental damage. Their efficient process significantly reduces the volume of contaminated material requiring further treatment, making it a valuable tool in environmental cleanup efforts.
For instance, a recent project in a lead-contaminated industrial site successfully removed over 80% of the lead using an ooze electro barrel system, demonstrating the potential of this technology in addressing complex environmental challenges.
Chemical Processing
In chemical processing, ooze electro barrels offer a precise method for conducting specific reactions. Their controlled electrochemical environment allows for the targeted modification of chemical compounds, offering a powerful tool for specific synthesis and purification processes. For example, in the production of pharmaceuticals, ooze electro barrels can be employed to purify active ingredients, enhancing the purity and efficacy of the final product.
This controlled environment also minimizes byproducts, resulting in a more sustainable and cost-effective production process. Furthermore, this precision allows for the development of new chemical compounds with unique properties, leading to innovative applications in diverse fields.
Operational Principles
Ooze electro barrels, a novel technology in material processing, leverage electrochemistry to achieve unique outcomes. Their operational principles rely on controlled electrochemical reactions within a specialized barrel-shaped container. Understanding these principles is crucial for optimizing performance and ensuring safe operation.
Electrochemical Reactions
The core of an ooze electro barrel’s operation hinges on electrochemical reactions. These reactions involve the transfer of electrons between different substances, often in the presence of an electrolyte solution. The electrolyte solution facilitates ion movement, which is vital for the overall reaction process. Anode and cathode components, immersed in the electrolyte, are crucial to the process.
Specific reactions vary based on the desired outcome. For example, if the goal is to enhance material breakdown, the reactions would focus on oxidation and reduction processes. If the objective is to modify material properties, the electrochemical processes would be adjusted to achieve specific reactions.
Energy Sources
Ooze electro barrels can utilize various energy sources, each impacting efficiency and cost. Direct current (DC) power supplies are essential for driving the electrochemical reactions. The power requirements depend on the scale of the operation, the material being processed, and the desired outcomes. Renewable energy sources like solar or wind power can be integrated to reduce environmental impact and operational costs.
The choice of energy source is a critical consideration for sustainability and economic viability.
Internal Components and Functions
The internal components of an ooze electro barrel are carefully designed to optimize the electrochemical process. A detailed illustration of the internal components would show a cylindrical barrel with electrodes positioned strategically within the barrel. The electrodes, typically made of conductive materials like titanium or stainless steel, are immersed in an electrolyte solution. The electrolyte solution, which facilitates ion movement, is crucial for efficient electrochemical reactions.
Sensors and monitoring systems are integrated to track critical parameters like temperature, voltage, and current. A robust sealing mechanism prevents leakage of the electrolyte solution, and the barrel itself is constructed from materials resistant to the corrosive nature of the electrolytic environment.
The electrodes are typically arranged in a specific configuration, like a series of concentric rings or a grid pattern, designed to maximize the surface area for the electrochemical reactions. This configuration increases the reaction rate and ensures even distribution of the current. The cylindrical barrel design facilitates efficient mixing of the electrolyte and the material being processed. The monitoring systems track the progress of the reactions, providing real-time data for process optimization.
The overall design emphasizes safety and efficiency for large-scale operations.
Diagram of Internal Components
(Note: A diagram cannot be included here. A visual representation of the barrel with labeled components – electrodes, electrolyte reservoir, DC power supply, monitoring system, and sealing mechanism – would be highly beneficial. The diagram should clearly illustrate the flow of current and the placement of electrodes to promote a comprehensive understanding.)
Safety and Maintenance
Ooze electro barrels, while offering significant advantages in various industrial applications, demand meticulous attention to safety and maintenance protocols. Neglecting these aspects can lead to severe accidents and equipment malfunction, impacting productivity and potentially endangering personnel. Understanding the potential hazards and implementing preventive measures is paramount for safe operation and long-term reliability.
Safety Precautions
Ensuring a safe working environment when handling ooze electro barrels necessitates stringent adherence to safety guidelines. Protective gear, such as safety glasses, gloves, and respirators, must be worn consistently to mitigate exposure to hazardous materials and potential electrical shocks. Clear signage indicating potential dangers and designated safety zones must be prominently displayed. Emergency procedures, including evacuation routes and first aid protocols, should be readily available and regularly reviewed.
Proper grounding procedures are crucial to prevent electrical shocks. Training programs for personnel handling ooze electro barrels are essential to ensure awareness of potential hazards and safe operating procedures.
Maintenance Procedures
Maintaining optimal performance of ooze electro barrels hinges on regular inspection and upkeep. A comprehensive maintenance schedule, including periodic visual inspections for wear and tear, should be established. Electrical components, including wires, connectors, and control panels, require careful examination for any signs of damage or degradation. Monitoring of fluid levels, ensuring they remain within the prescribed operating parameters, is essential to avoid overheating or other operational issues.
Regular cleaning and maintenance of the barrel’s exterior and interior are necessary to prevent the buildup of contaminants or corrosion. Any unusual sounds, smells, or vibrations should be immediately investigated and addressed by qualified personnel.
Potential Hazards
Ooze electro barrels present several potential hazards. The corrosive nature of the ooze necessitates careful handling and appropriate protective measures. Electrical hazards, including the risk of electrocution, must be mitigated by employing proper grounding and insulation techniques. Improper disposal of the ooze or its byproducts can lead to environmental contamination. Overheating of the barrel, due to improper maintenance or operational issues, can pose a fire hazard.
Improper handling of the barrel or its contents can result in physical injury. Improper grounding, in particular, is a significant concern, as it can lead to electrical shocks and equipment malfunctions.
Regular Maintenance Checklist
This checklist provides a structured approach to ensuring the continued safe and efficient operation of ooze electro barrels. Regular inspections are crucial to maintaining optimal performance.
- Visual Inspection: Check for any signs of wear, tear, corrosion, or damage on the barrel exterior and internal components. Pay close attention to electrical connections, seals, and fluid levels.
- Electrical System Check: Verify proper grounding and insulation of all electrical components. Test the functionality of the control panel and any safety mechanisms.
- Fluid Level Monitoring: Confirm that the fluid levels remain within the prescribed operating range. Ensure proper fluid composition and identify any signs of contamination.
- Cleaning and Sanitation: Clean the barrel’s exterior and interior, following established protocols. Ensure thorough removal of any contaminants or buildup.
- Safety Gear and Training: Verify that all personnel have the necessary safety equipment and have received adequate training on safe operating procedures.
- Record Keeping: Document all maintenance activities, including inspections, repairs, and adjustments, in a logbook for future reference.
Historical Context
The development of ooze electro barrels reflects a continuous evolution in materials science, engineering, and energy storage. Early iterations, while rudimentary, laid the groundwork for the sophisticated devices used today. This evolution is marked by incremental advancements, driven by the need for greater efficiency, safety, and reduced environmental impact.The fundamental concept of using electrochemistry to manipulate ooze-like substances for energy storage has been a subject of research for decades.
Initial experiments focused on understanding the behavior of ooze in controlled electric fields. Over time, these experiments evolved into more complex designs, leading to the current generation of ooze electro barrels.
Early Experiments and Prototypes
Early experiments with ooze electro barrels primarily focused on the fundamental interactions between ooze and electric fields. These experiments, conducted in the late 20th century, were often limited by materials science constraints and a lack of precise control over the ooze composition. Results from these initial experiments, while not immediately applicable, provided valuable insight into the basic principles governing the system.
Key Advancements in Ooze Electro Barrel Technology
Several key advancements have shaped the modern ooze electro barrel. These include improvements in:
- Ooze Formulation: Early ooze formulations were often unstable and prone to degradation. Modern research focuses on creating stable, high-performance ooze formulations capable of withstanding repeated charge/discharge cycles. This stability has been a critical factor in the advancement of the technology.
- Electrode Materials: The development of novel electrode materials, capable of enhancing the interaction with the ooze, has significantly increased the energy density and efficiency of the barrels. This is particularly crucial for the deployment of the ooze electro barrel in high-demand applications.
- Control Systems: Advanced control systems have enabled more precise control over the charging and discharging processes, minimizing energy loss and extending the operational lifespan of the ooze electro barrel. The improved control is essential to optimize performance and safety.
Influential Factors Shaping Ooze Electro Barrel Design and Use
Several factors have shaped the design and application of ooze electro barrels:
- Environmental Concerns: The increasing awareness of environmental issues has driven research into more sustainable and environmentally friendly ooze electro barrels, focusing on the reduction of harmful byproducts.
- Energy Storage Demands: Growing energy storage needs, particularly in renewable energy systems, have fueled the development of higher-capacity and more efficient ooze electro barrels.
- Cost Considerations: The cost-effectiveness of the manufacturing process and the overall cost of the ooze electro barrel play a significant role in its market viability.
Timeline of Ooze Electro Barrel Development
Year | Event | Significance |
---|---|---|
1980s | Initial experiments with ooze and electric fields. | Fundamental research into ooze-electric interactions. |
1990s | Development of early prototypes with limited performance. | Early iterations and identification of critical challenges. |
2000s | Significant improvements in ooze formulation and electrode materials. | Increased energy density and efficiency. |
2010s | Implementation of advanced control systems. | Enhanced performance and safety. |
2020s | Focus on sustainability and cost-effectiveness. | Expanding market applications and wider adoption. |
Design Considerations
Ooze electro barrels, crucial components in advanced industrial processes, require meticulous design considerations to ensure optimal performance, safety, and longevity. Their design must balance the need for robust containment with the demands of efficient electrochemical reactions. This necessitates careful attention to material selection, structural integrity, and operational parameters.
Fundamental Design Principles
The design of ooze electro barrels is governed by several fundamental principles. First, the barrel’s structure must withstand the intense pressures and forces generated during the electrochemical reactions. Second, the material selected must resist corrosion and degradation in the corrosive electrolyte solutions. Third, the barrel’s design must allow for easy and safe access for maintenance and inspection. Finally, the design must facilitate efficient heat dissipation to prevent overheating, which can compromise the barrel’s integrity and the efficiency of the process.
Factors Influencing Size, Shape, and Material Selection
The size, shape, and material selection of ooze electro barrels are significantly influenced by the specific application and the electrochemical reaction parameters. Larger barrels are required for higher throughput processes, while smaller barrels are more suitable for laboratory-scale experiments. The shape of the barrel can affect the distribution of current and the uniformity of the electrochemical reaction. Material selection is critical, as the electrolyte can be highly corrosive.
Materials like specialized alloys with high corrosion resistance, such as certain stainless steels or nickel-based alloys, are often employed. Considerations also include the barrel’s ability to withstand thermal gradients, especially in continuous operation.
Ensuring Durability and Longevity
Durability and longevity are paramount in ooze electro barrel design. This involves meticulous material selection, structural reinforcement, and appropriate stress analysis. To mitigate corrosion, specialized coatings or linings can be employed, such as ceramic or polymer-based coatings. Regular inspections and maintenance protocols, as well as the design of easily accessible components, are essential for proactive maintenance. Careful consideration must be given to potential wear points, like the contact points between the barrel and electrodes, and measures taken to extend the life of these parts.
Design Parameters and Performance Impact
Design Parameter | Impact on Performance |
---|---|
Barrel Thickness | Higher thickness improves structural integrity, but increases weight and cost. Impacts pressure resistance. |
Electrode Material | Proper electrode material choice is crucial for reaction efficiency and minimizes corrosion at contact points. |
Electrolyte Composition | The chemical composition of the electrolyte directly impacts corrosion rates and the required material properties for the barrel. |
Cooling System Design | Effective cooling systems prevent overheating and ensure reaction consistency, thus affecting barrel longevity. |
Access Ports and Fittings | Well-designed access points enable easy maintenance and inspection, reducing downtime and extending barrel lifespan. |
Materials and Components
The construction of an ooze electro barrel necessitates a careful selection of materials to withstand the unique operating conditions, including high pressures, corrosive environments, and electrical currents. Choosing the right materials ensures the barrel’s longevity, safety, and efficiency. The precise composition and properties of each material directly impact the barrel’s overall performance and suitability for various applications.
Material Selection Criteria
Material selection for ooze electro barrels is guided by several crucial factors. These include resistance to corrosion from the ooze itself, electrical conductivity for efficient operation, structural integrity under pressure, and compatibility with any necessary coatings or seals. The choice of material must also consider cost-effectiveness and availability. A thorough understanding of the specific operating environment, including the type of ooze, the expected pressure and temperature ranges, and the electrical parameters, is vital for optimal material selection.
Materials Used in Ooze Electro Barrels
The construction of an ooze electro barrel typically involves a combination of materials. The primary components are often selected based on their specific properties and suitability for the application. Common materials include high-strength alloys, corrosion-resistant metals, and specialized polymers.
List of Materials and Their Properties
- Steel Alloys: High-strength steel alloys, such as stainless steel (e.g., 316L), are frequently employed due to their excellent resistance to corrosion and high tensile strength. Their ability to withstand pressure and maintain structural integrity is paramount. Stainless steel’s passivity in corrosive environments is a significant advantage.
- Aluminum Alloys: Lightweight aluminum alloys, with specific compositions, can be used in applications where weight reduction is crucial. Their corrosion resistance, however, might require additional protective coatings. Consideration must be given to the specific type of ooze and its potential corrosive effects.
- Polymers: High-performance polymers, like certain types of polyolefins or fluoropolymers, are employed for specific components, especially where chemical resistance is paramount or for sealing purposes. Their resistance to the ooze’s specific chemical composition is a crucial factor. Polymers’ durability and resistance to degradation are essential for long-term performance.
- Electrical Conductive Materials: Materials like copper or nickel-plated steel are vital for the electrical components within the barrel. Their conductivity is essential for efficient current flow and must be carefully selected based on the expected electrical load and the corrosive nature of the ooze.
- Coatings and Seals: Corrosion-resistant coatings, often applied to the interior and exterior surfaces of the barrel, play a vital role in preventing corrosion and extending the barrel’s lifespan. The type of coating must match the specific chemical composition of the ooze. Suitable seals, designed for high pressure and chemical compatibility, are necessary to prevent leakage.
Material Selection Table
Material | Property | Application in Ooze Electro Barrel |
---|---|---|
Stainless Steel 316L | High tensile strength, excellent corrosion resistance | Barrel body, structural components |
Aluminum Alloy 6061 | Lightweight, moderate corrosion resistance | Barrel body (where weight is critical), internal components |
Polytetrafluoroethylene (PTFE) | Excellent chemical resistance, low friction | Seals, gaskets, liners |
Copper | High electrical conductivity | Electrical conductors, terminals |
Epoxy Coating | Excellent adhesion, chemical resistance | Interior and exterior coatings for corrosion protection |
Future Trends and Innovations
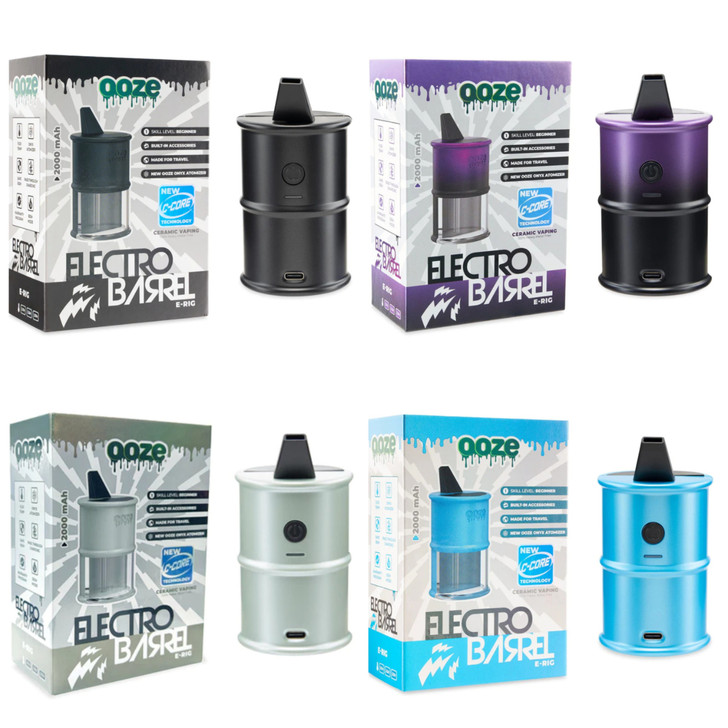
The ooze electro barrel market is poised for significant transformation driven by evolving technological advancements and market demands. Increased focus on sustainability, performance optimization, and enhanced safety protocols will shape future designs and applications. This dynamic environment presents both challenges and opportunities for manufacturers and users alike.
Potential Developments in Materials and Components
Materials science advancements are likely to lead to barrels featuring enhanced corrosion resistance, improved conductivity, and lighter weight. The integration of advanced composite materials, incorporating carbon fiber or other high-strength polymers, could drastically reduce the barrel’s weight without sacrificing structural integrity. This development would be particularly valuable in applications demanding portability and ease of handling. Furthermore, incorporating self-healing materials within the barrel’s structure could significantly extend its lifespan by automatically repairing minor damage.
Emerging Trends in Operational Efficiency
Smart technologies, such as embedded sensors and real-time monitoring systems, are poised to optimize the operational efficiency of ooze electro barrels. These systems can track operating parameters like pressure, temperature, and current flow, enabling predictive maintenance and reducing downtime. Remote monitoring capabilities will allow operators to proactively address potential issues before they escalate, thereby enhancing operational reliability. The implementation of automated control systems could further streamline processes and reduce manual intervention.
Innovations in Safety and Maintenance
Safety remains paramount in the evolution of ooze electro barrel technology. Future designs will likely incorporate enhanced safety features, such as improved containment systems, fail-safe mechanisms, and automatic shut-off protocols in response to critical parameters. Predictive maintenance algorithms, fueled by sensor data, will allow for proactive maintenance schedules, reducing the risk of unexpected failures and minimizing downtime. These advancements will not only improve safety but also significantly lower operational costs in the long run.
Potential Future Developments
- Advanced Materials: Integration of self-healing composites, enhanced corrosion-resistant alloys, and lightweight materials to improve durability and reduce weight.
- Smart Technologies: Implementation of embedded sensors, real-time monitoring systems, and predictive maintenance algorithms to optimize performance, enhance safety, and minimize downtime.
- Automated Control Systems: Development of automated control systems to streamline processes, reduce manual intervention, and increase operational efficiency.
- Enhanced Safety Features: Incorporating improved containment systems, fail-safe mechanisms, and automatic shut-off protocols for enhanced safety during operation.
- Sustainable Practices: Exploration of eco-friendly materials and manufacturing processes to reduce environmental impact.
Outcome Summary
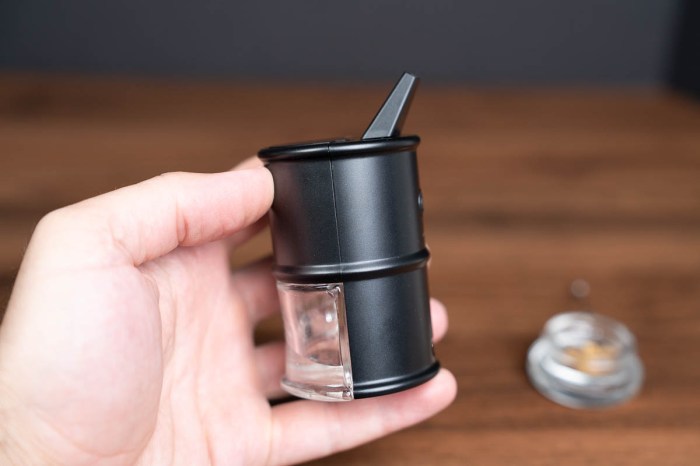
In conclusion, the ooze electro barrel, with its unique properties and applications, promises to be a transformative technology. Its intricate design and sophisticated operational principles offer significant potential, while safety and maintenance considerations are critical for responsible deployment. Future trends and innovations will be crucial in shaping the evolution of this intriguing technology.